Dexterous robot-arm control with vision, without calibration.
The “CREWBO” industrial robot control software achieves projects that were difficult to achieve in the past with real-time visual feedback control.
What is real-time visual feedback control?
This method controls the robot by focusing only on the relative position/posture information of the object and at the fingertips. It does not accumulate errors in coordinate transformation, and the coordinate system of the camera and robot can deviate significantly from the assumed set position/posture without any problems at all.
The work can be executed as long as the robot can reach it, without having to strictly position the robot, camera, workpiece, etc.
A complete software, ready to use on Day 1
1No burden of calibration
The burden of camera and robot calibration is eliminated, saving cost and time in building highly accurate robotic systems that can be used without a fixed environment.
Control is possible even in rough environmental settings, improving the robot’s ability to adapt to the site. Since it can be used without a fixed environment, it can achieve high-precision control of AGVs and dolly-mounted robots as well as sites where cameras and robots cannot be fixed.
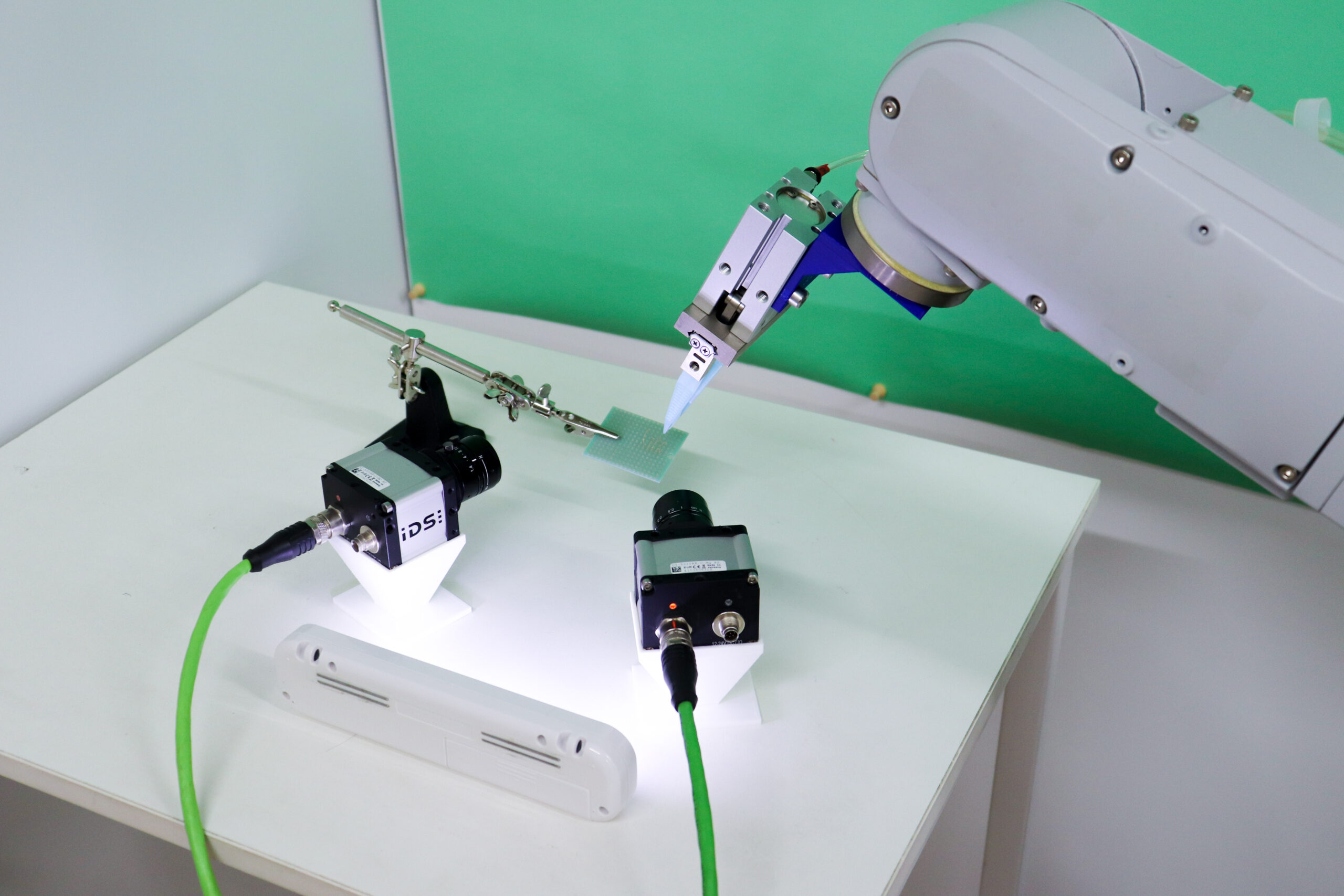
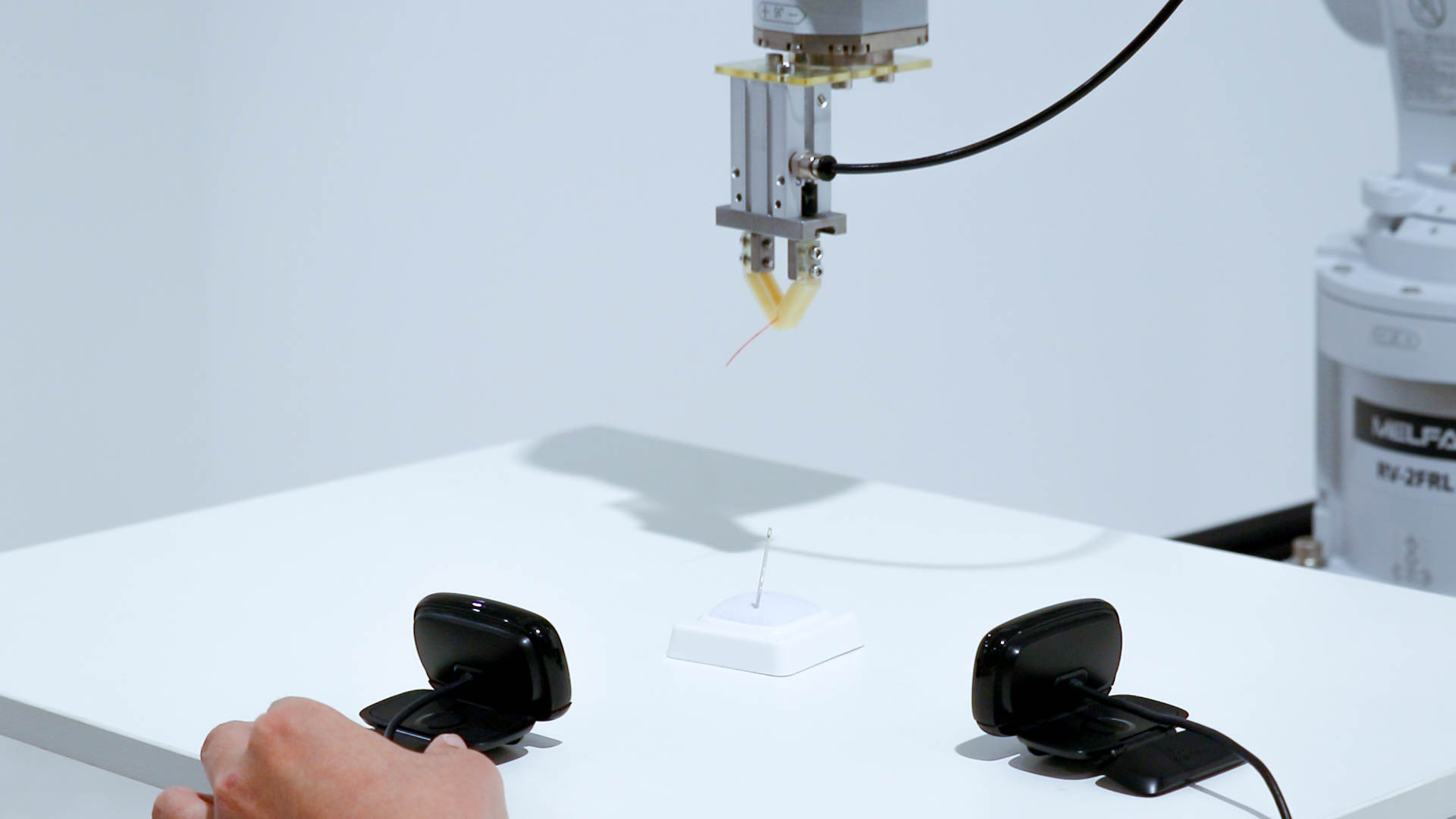
2High-precision control
Continuously adjusts forearm control based on camera images for easy, high-precision control.
With a fingertip control accuracy of 0.02 mm, even flexible objects that deform and fluctuate can be handled with high precision. Simultaneous control of robots from multiple manufacturers and insertion operations without force sensors are also possible.

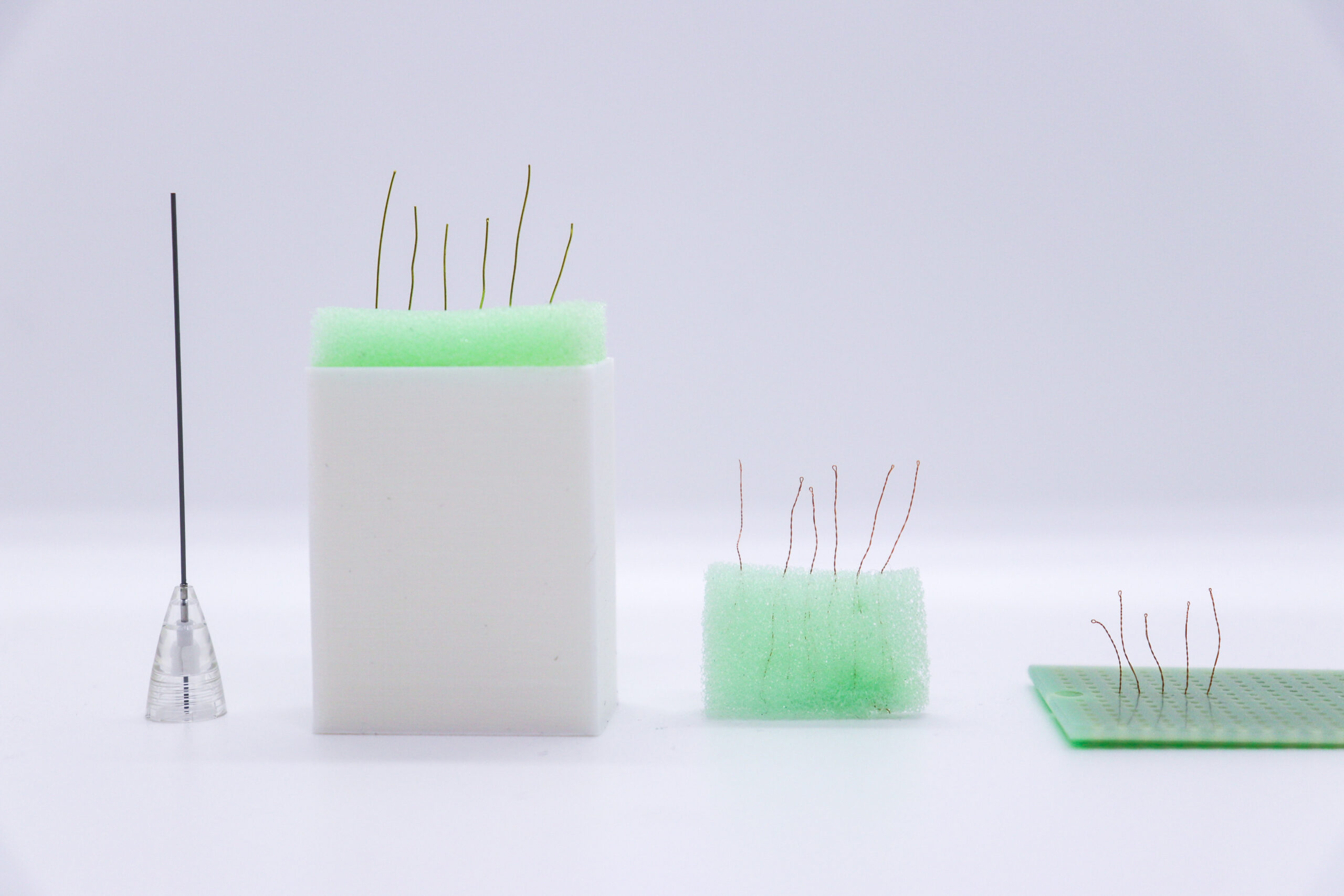
3High speed and smooth operation
Constant adjustment of control commands to the robot reduces takt time by controlling sway, and reduces rattling by controlling acceleration.
CREWBO automatically adjusts control commands to the robot and changes the trajectory in real time, allowing for fast pick-and-place and fast, smooth tracking.


Included items
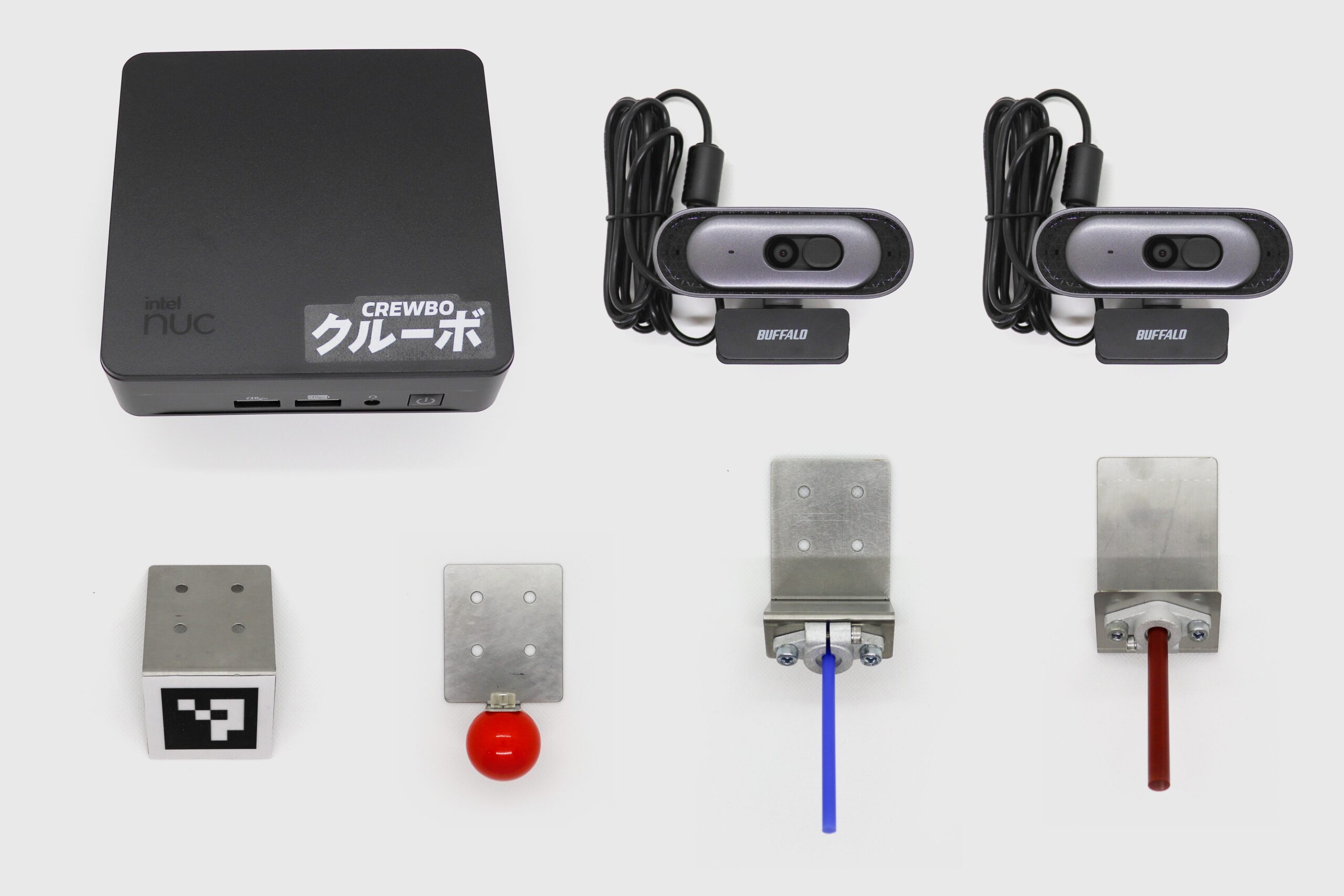
Crewbo comes standard with a control computer with all the necessary software installed, sample hands used in tutorials, USB cameras that can be used for various controls, and a startup guide.
-
Crewbo installed control computer: 1 unit
-
USB cameras: 2
-
Robot hands: 4 types
-
Startup guide: Approximately 180 pages (data)
*The appearance of the control computer may change.
Example of system configuration
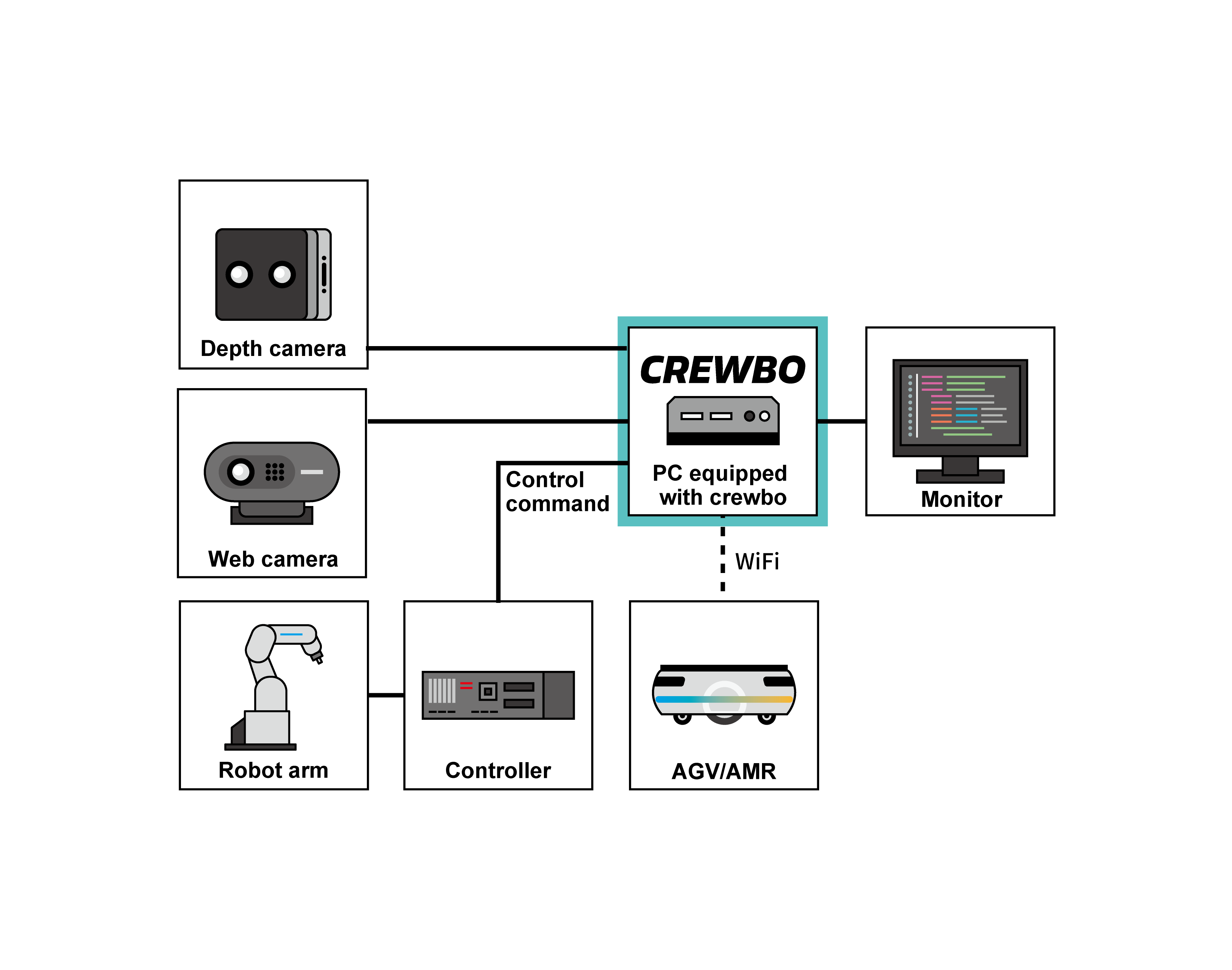
-
Select and insert LEDs using a depth camera.
-
Correcting the LED posture using a web camera.
-
AMR controlled by WiFi.